Yusen Logistics improves visibility and efficiency with DexoryView
August 29, 2024
Yusen Logistics, a global leader in supply chain solutions, sought to improve service delivery for its end customers, including leading electronics manufacturers, by investing in digitalisation and automation. To achieve this, Yusen Logistics partnered with Dexory to deploy the DexoryView platform, aiming to enhance real-time inventory visibility and operational efficiency.
The challenge
Yusen Logistics faced several critical challenges in its pursuit of operational excellence:
- Improving customer service: With a commitment to constantly enhancing its services, Yusen Logistics needed a solution that could provide real-time visibility of inventory to its customers, ensuring transparency and reliability.
- Reducing manual labour: The traditional manual processes of inventory management were time-consuming and labour-intensive, requiring over 100 hours of work per month for wall-to-wall checks. This process was not only inefficient but also led to a pressurised working environment and the need for overtime.
- Maintaining high standards: Yusen Logistics aimed to maintain high standards of warehouse cleanliness and labelling consistency, which are crucial for efficient operations and customer satisfaction
Providing the solution
Yusen Logistics implemented the DexoryView platform in April 2024, transforming its inventory management and warehouse operations.
Rapid wall-to-wall scans
With DexoryView, Yusen Logistics can now conduct comprehensive wall-to-wall scans of its entire warehouse within just two hours each day. This is a significant improvement over the previous process, which took over 1.5 weeks per month and required extensive manual labour.
Eliminitation of annual checks
The generation of real-time data each day has allowed Yusen Logistics to completely remove the need for annual wall-to-wall checks, saving an additional 205 hours of work each year.
Improved team morale
The reduction in manual labour and overtime has led to increased team morale and productivity. The pressurised environment has been alleviated, allowing the team to focus on more strategic tasks.
Enhanced operational efficiency
The first two weeks of using DexoryView saw a noticeable improvement in overall warehouse cleanliness and labelling consistency, which contributed to greater operational efficiency.
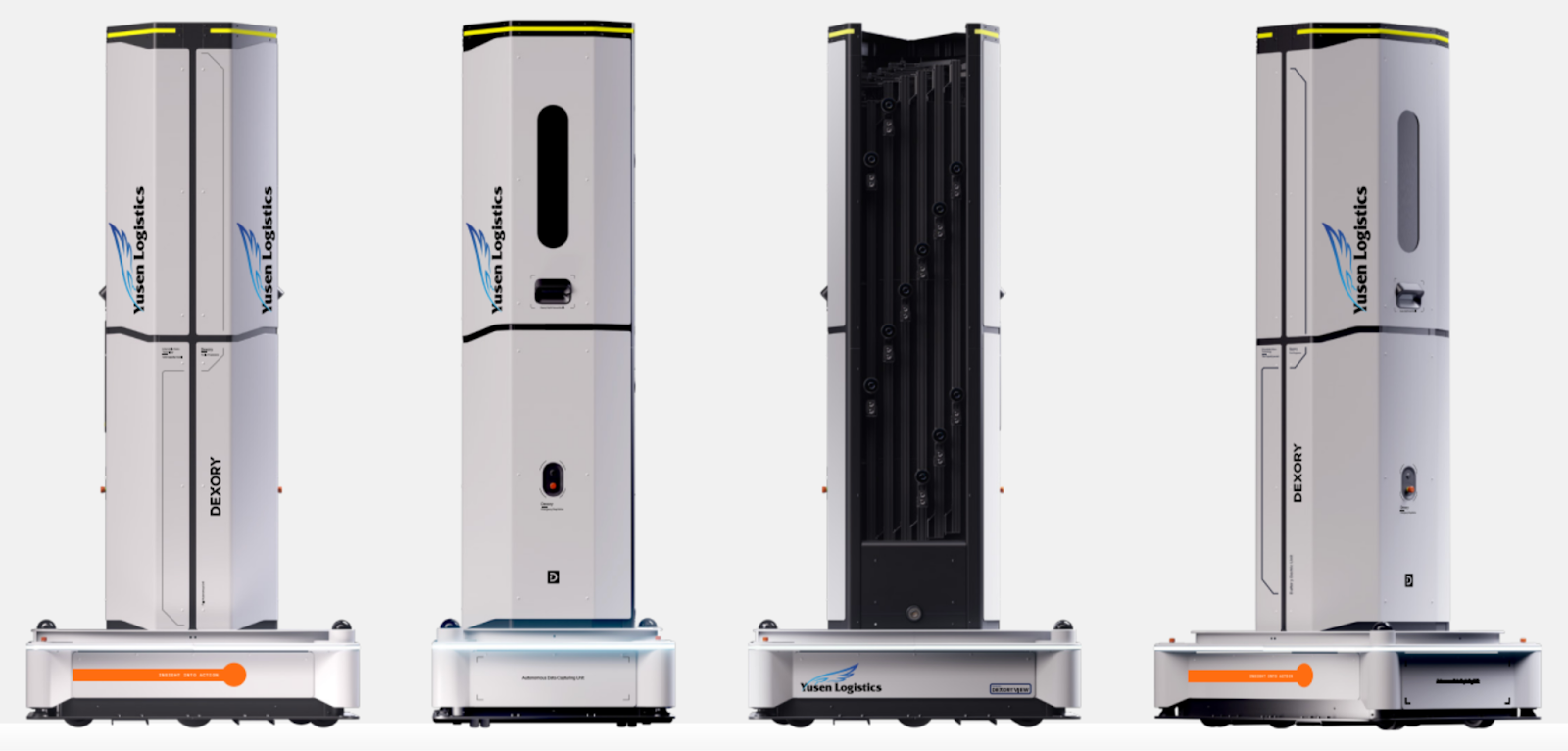
Key impact and achievements
The implementation of DexoryView at Yusen Logistics delivered remarkable results:
- Significant time savings: Wall-to-wall counting time was reduced from 100 hours per month to just 2 hours, allowing for daily inventory checks. This represents a reduction of 98 hours per month.
- Zero lost items: The enhanced visibility and accuracy provided by DexoryView resulted in zero lost items, ensuring that inventory levels were always precise.
- Rapid discipline change: Within two weeks, Yusen Logistics achieved increased warehouse cleanliness and labelling consistency, which are crucial for maintaining high operational standards.
“The use of robotics and automation helps to optimise our warehouse space, which reduces costs, improves performance and stock accuracy, and removes downtime for manual stock takes.” — Darren Felstead, Head of Contract Logistics, Yusen Logistics
Conclusion: Commitment to technological advancement
By deploying DexoryView, Yusen Logistics not only optimised its warehouse operations but also significantly improved its service delivery to customers. This partnership highlights the importance of embracing technology to drive efficiency, reduce costs, and enhance overall performance.