The true value of inventory automation in warehousing: Unlocking quick ROI
January 13, 2025
With increasing complexity, faster-moving supply chains, and the need for greater accuracy, the pressure for warehouses to innovate has never been higher. This is where warehouse automation steps in, not just as a solution, but as a strategic enabler that delivers quick ROI (Returns On Investment) and unlocks long-term benefits.
Maria Torrent-March, Managing Director at Iron Mountain, recently joined Dexory’s Co-founder and Chief Commercial Officer Oana Jinga for a lively discussion on this very topic. Their conversation highlighted how automating inventory scanning can transform warehouses. Here’s what they shared.
Why accuracy matters for ROI in warehousing
“Accuracy is incredibly important,” Maria emphasised during the webinar. “Not just for running a warehouse efficiently, but also for enabling customers to run their businesses effectively.”
Warehouses are busy places. Pallets are constantly moving in and out. Mistakes in inventory can delay orders, mess up workflows, and upset customers. Traditional methods, like manual inventory checks, can’t keep up. They take too much time and don’t give a full picture of what’s happening. This is where automated solutions like warehouse robots can step in to bridge the gap.
Automation solves these problems. For example, Dexory’s robot can scan up to 10,000 pallet locations an hour. It sends the data straight to a platform where you can see everything in real-time. This has helped Iron Mountain achieve top-level accuracy and quick ROI, even in complex warehouses. Real-time visibility into inventory means fewer errors, smoother workflows, and happier customers.
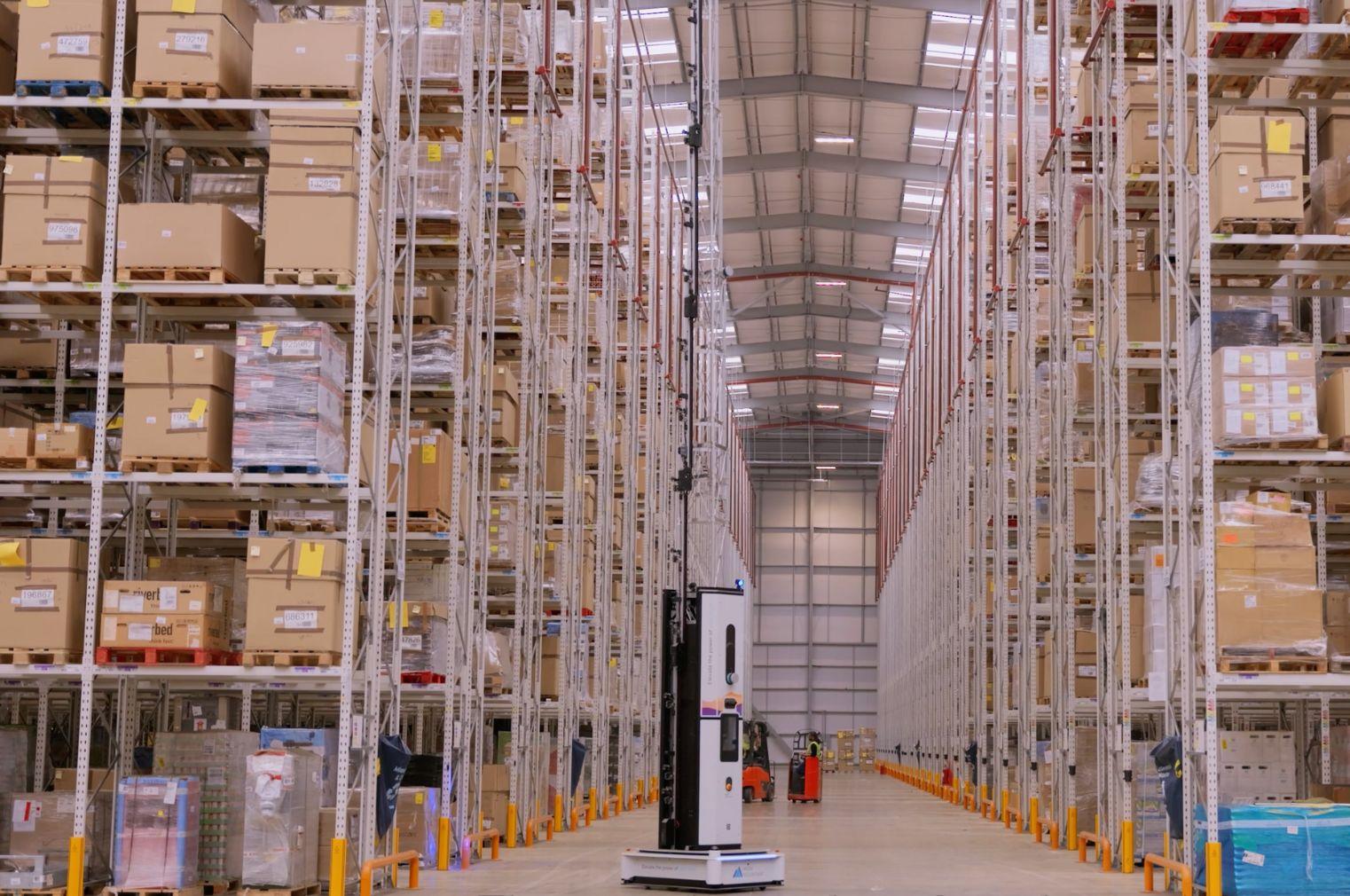
ROI in warehouse automation: Fast, clear benefits
One key point from the webinar was how quickly companies can see ROI with automation. Oana highlighted a critical advantage: “When people think about automation projects, they often assume long timelines. We’ve worked hard to address that head-on, ensuring value is delivered very quickly.”
Maria shared how Iron Mountain built their business case for adopting Dexory’s solution:
1. Time saved: “We compared how many people we’d need to recruit for manual inventory management versus the efficiency of the robot. The time saved on cycle counts and error investigations was a game-changer.”
2. Error reduction: Mistakes happen in every warehouse, but catching and correcting them swiftly is vital. Maria explained that “errors left unaddressed can disrupt picking and put-away processes, impacting the entire operation.”
3. Resource optimisation: Automating repetitive tasks frees up valuable resources. As Maria put it, “We want our teams and equipment focused on revenue-generating activities, not just checking for the sake of checking.”
More than ROI: Extra value from inventory automation
While warehouse automation, especially inventory scanning, is a core function, its impact extends far beyond.
1. Space optimisation: Maria noted how having a digital twin of the warehouse provides unparalleled visibility. “No more manual mapping or piecing together reports. We can make better decisions about rack adjustments and space allocation,” she explained. This visibility is key to making better decisions about layout and storage.
2. Cross-site visibility: With Iron Mountain operating multiple sites, the ability to monitor stock across locations has been transformative. “The platform helps us decide where to move stock and provides customers with real-time insights,” Maria added. This capability is especially useful for businesses managing large inventories across different regions.
3. Customer confidence: Automation also enhances Iron Mountain’s relationships with customers. “They see the level of accuracy and innovation we bring, and it sets us apart,” Maria shared. Oana chimed in, adding, “Our collaboration shows how automation can drive customer satisfaction and build credibility.” Satisfied customers often lead to repeat business and stronger partnerships.
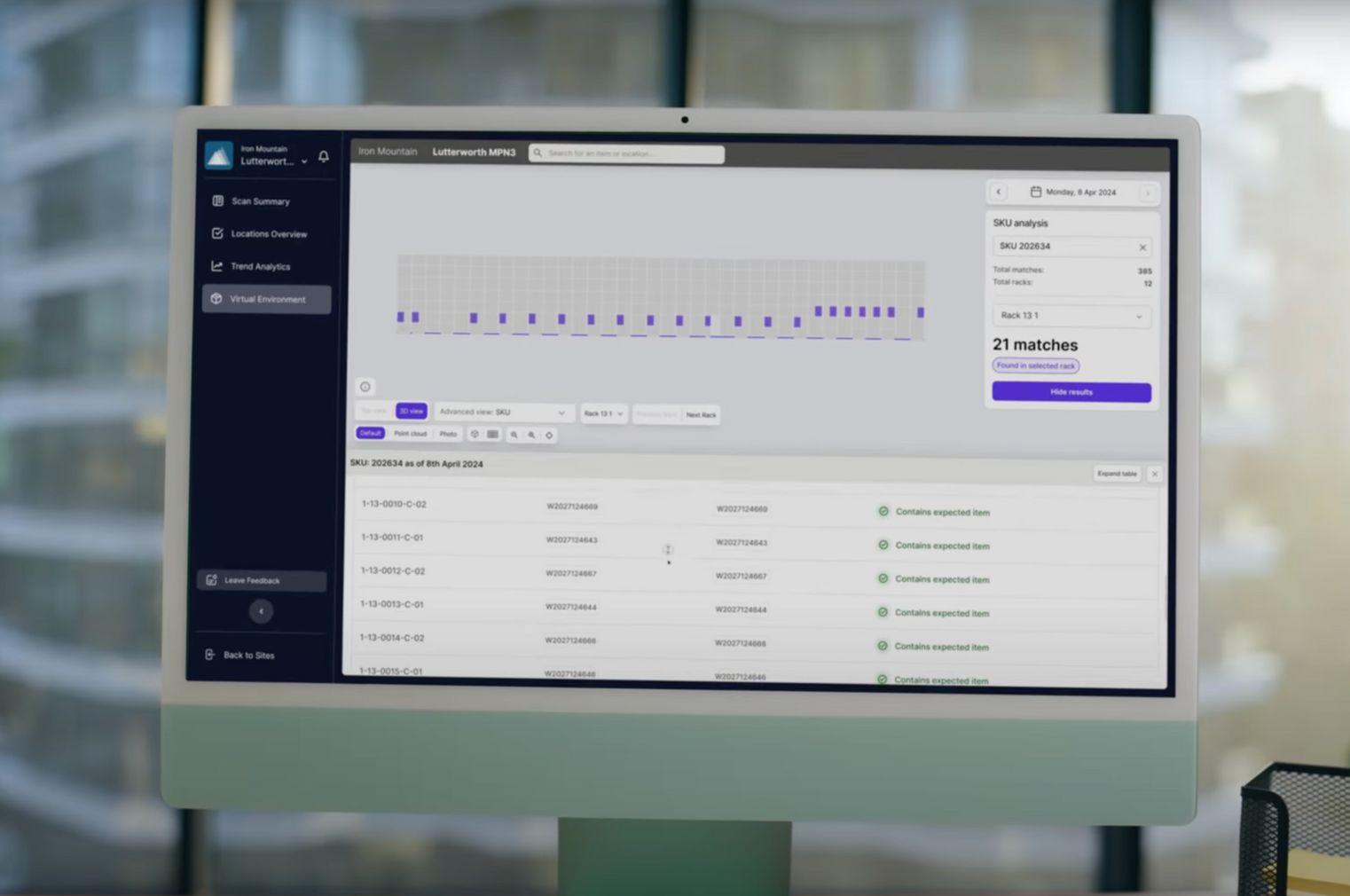
How warehouse automation helps people, not replaces them
Both Oana and Maria agreed that automation doesn’t replace people, it empowers them. “By taking on repetitive, mundane tasks, automation allows our teams to focus on more meaningful, strategic work,” Maria pointed out. This shift not only increases job satisfaction but also helps employees develop new skills that add value to the company.
By reducing the physical and mental strain of repetitive tasks, automation creates a healthier, more productive work environment. In fact, automated systems often work best when paired with human oversight, ensuring operations run smoothly and efficiently.
For businesses considering automation, Maria offered a piece of advice: “Think beyond the technology itself. Look at how it integrates into your operations and the broader value it can unlock. With the right approach, it’s not just an investment in efficiency but in your company’s future.”
Conclusion: ROI from warehouse robots
From accelerating inventory processes to enabling strategic decision-making, warehouse automation and robots delivers quick ROI in ways that ripple across the entire business. And as Iron Mountain’s journey shows, the benefits go beyond financial gains to include operational resilience, enhanced customer relationships, and empowered teams.
As Oana summed it up: “When you’re able to deliver value quickly, while also future-proofing your operations, it’s a win for everyone involved.”