The robotics behind Dexory’s automated inventory management system
July 10, 2024
Over the last few years, rapid development in robotics technology has led to a robot revolution in the logistics industry. Today’s machines are more intuitive, complex and autonomous than ever, helping warehouses increase productivity by approximately 25% to 70% [1]. Consequently, it is predicted that over 4 million robots will be operating in 50,000 warehouses by 2025 [2]. This impressive surge in automation is allowing warehouses to respond to the rising demands of e-commerce, whilst coping with labour and space shortages.
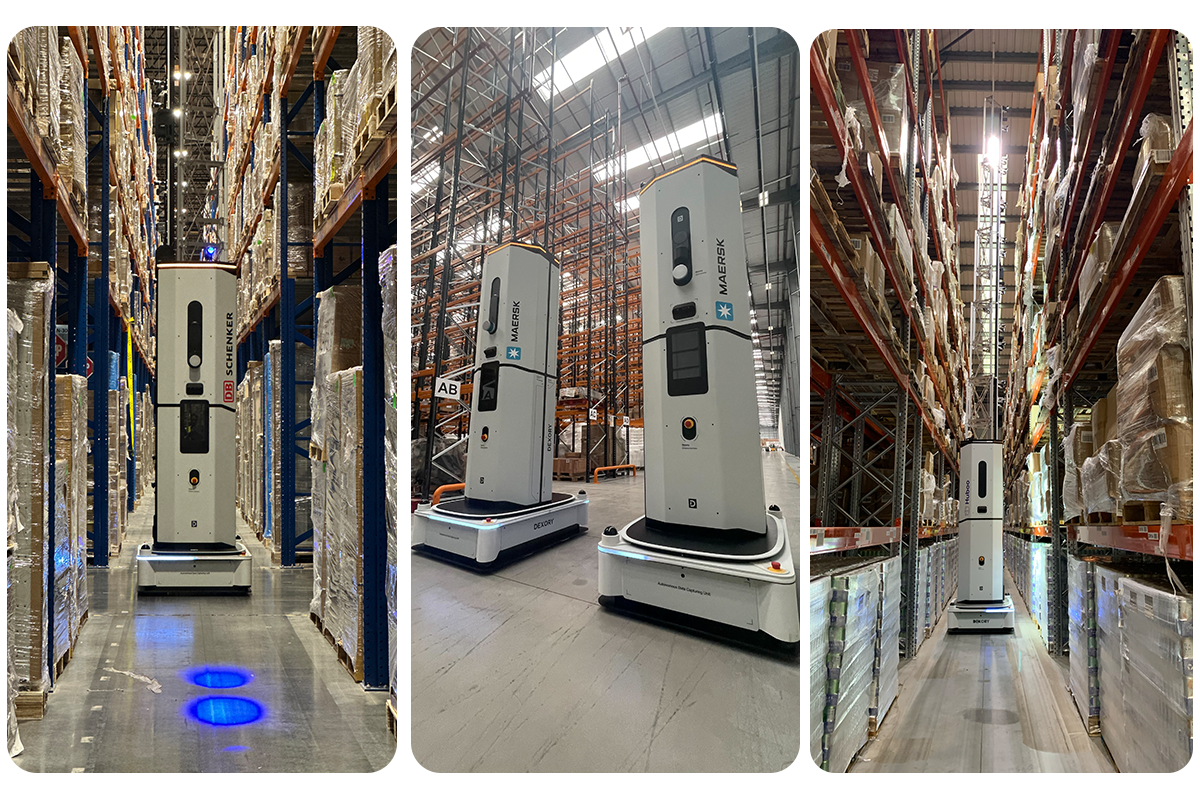
There are now many types of robots utilised in warehouses, but the most advanced are Autonomous Mobile Robots (AMRs). AMR robots can observe, understand and navigate through its environment independently, without any human intervention or control. This means they can quickly and reliably automate low skill, repetitive tasks such as the transportation of inventory, order picking and sorting.
How does an autonomous robot work?
When a robot moves autonomously from one location to the next, it runs through five main processes:
- Mapping – the robot uses sensors to map its surrounding environment
- Localisation – algorithms interpret this information and constantly calibrate its position and orientation relative to this map
- Path planning – plans its trajectory to the desired location
- Navigation – the robot moves along this path, avoiding any obstacles on route
‘If you wish to travel from one city to another, you need a map of how to get there, you need to know where you currently are and then you need to understand how your position changes as you move – it is exactly the same with autonomous robots,’ says Dr Marcus Scheunemann, Head of Autonomy at Dexory.
‘However, achieving this in a warehouse is extremely challenging. Warehouses may appear static, but the constant movement of inventory, machinery and staff make it a very dynamic environment with a huge level of similarity. Our goal is to develop a truly autonomous robot that can accurately navigate itself around any warehouse whilst continuously reacting to its surroundings. This makes our robot much more reliable, easy to install and completely independent.’
The Dexory robot
To help warehouses automate their operational processes, Dexory have developed an innovative solution that combines advanced AMR technology with digital twin software. The AMR robot features an extendable 12 m tower which mounts an array of sensors, cameras and lidars. As the robot moves along the aisles of a warehouse, these perception systems scan every location on a rack, simultaneously within seconds.
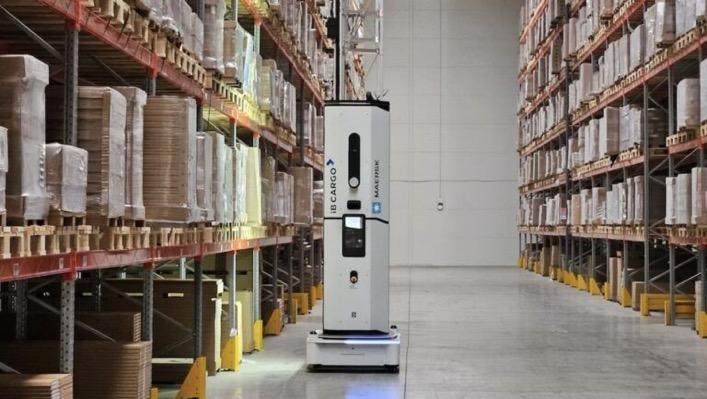
This data is then fed into a software platform called DexoryView which creates a digital twin of the warehouse. Staff can interact with this virtual model to quickly understand stock levels, capacity and the opportunities to improve efficiency.
- Discover how Dexory's automated warehouse inventory management works: Read more
Mapping
The first step to achieving complete autonomy is programming the robot to understand its exact position relative to its surroundings. ‘This is particularly difficult for warehouse robots, because there is no GPS inside a warehouse,’ explains Dr Guillaume Doisy, Lead Architect at Dexory. ‘Even if there is a signal, GPS is only accurate to a few metres, and we need much higher accuracies to centimetres.’
The alternative is to use a map of the warehouse which the robot can constantly reference. Typically, this is a 2D map that is constructed during initial deployment. However, with pallets, loading areas and other obstacles constantly changing, this map can quickly become unreliable and need updating.
‘Remapping requires the robot to run often enough to maintain an updated map and if for some reason it doesn’t, the map will be out of date and cause the robot to be disorientated on its next outing,’ highlights Doisy.
‘Whereas we have developed a unique mapping approach which combines both 2D and 3D data to generate a blueprint of the warehouse that remains stable over time. This is incredibly powerful because it means our robot can cope with the dynamic environment of a warehouse, without ever having to remap.’
With no remapping necessary, Dexory can deploy its robots fast, even on large sites, without the need for expensive technical personnel to be involved in the process.
Localisation
Once the initial map of the warehouse has been created, the robot then needs to understand its position on that map. With no GPS, most AMRs augment the environment with markers on the floor, or barcodes on the racks. However, these must be installed and calibrated in the warehouse, which can prove costly, time consuming and difficult to scale on large warehouses. Furthermore, these references can often be incorrect and wear away over time.
‘Instead, we use a combination of 3D cameras, 2D safety lidars and 3D lidars to capture a field of view up to 50 m [164 ft] horizontally and 25 m [82 ft] vertically around the robot,’ reveals Doisy. ‘Our innovative localisation techniques can then interpret this information, so the robot understands its exact position, without having to make any modification to the infrastructure of the warehouse.’
‘To the best of my knowledge, thanks to our proprietary localisation technology, we are the only mobile robotics company capable of maintaining worry free robust robot localisation over time in the dynamic warehouse space.’
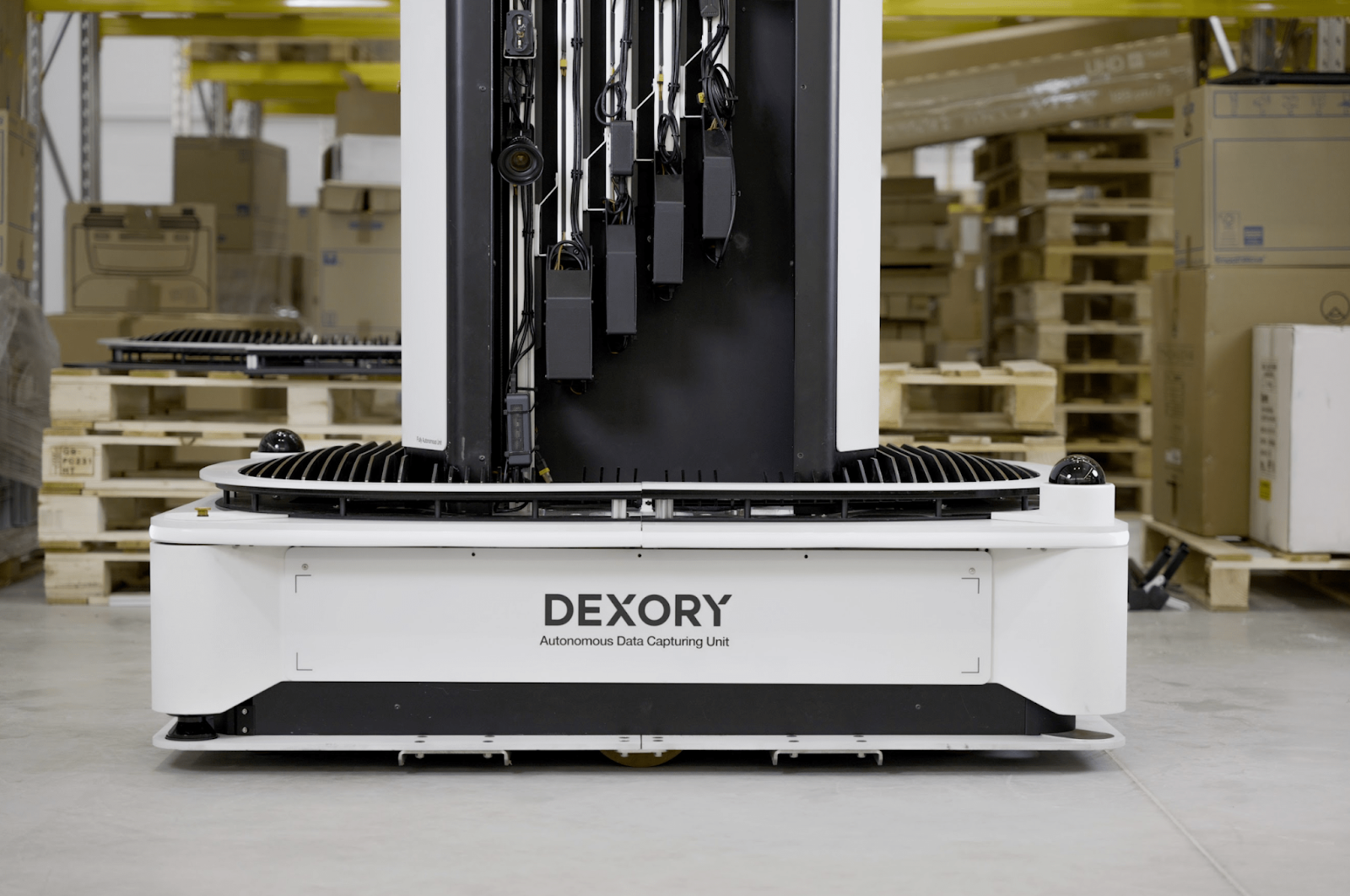
This localisation process runs continuously whenever the robot is in operation. This ensures the robot constantly understands its position relative to its surroundings, which is essential to achieving precise manoeuvrability.
Path planning
Now the robot knows the layout of the warehouse and its position, it can start to plan its initial route. However, scanning an entire warehouse can involve hundreds of aisles, so Dexory define a schedule for the robot to follow. This schedule consists of a number of missions, where each mission involves scanning both racks in an aisle.
When the robot receives a command to start a mission, it computes the optimum trajectory from its current position to the goal position. This is defined as the global path and is based on the reference map, so any static obstacles detailed on this map are avoided.
Navigation
Once the robot has determined its global path, PID (Proportional Integral Derivative) controllers drive the wheels to follow this route. These controllers are constantly comparing the information from the lidars and cameras with the global path. If a dynamic obstacle, such as a forklift or pallet, intrudes its trajectory, it is immediately detected, and the robot stops.
Lidars help the robot to detect and avoid dynamic obstacles immediately
‘The robot then waits a few seconds to see if the obstacle moves, and if not, recalculates a new trajectory back to its global path,’ explains Doisy. ‘In this way, the robot can move autonomously around a warehouse in a safe manner, avoiding any obstacles at ground level but also high up in the racks.’
Working in harmony
The five stages of mapping, localisation, path planning, navigation and relocalisation are bought together by a control system which orchestrates these processes to work simultaneously. This results in a truly autonomous robot that navigates a warehouse, automatically extends the tower to the desired height, scans an aisle and returns to its dock, all whilst avoiding obstacles.
‘At every moment in time, the robot is merging all these streams of information and computing a decision about the action it will take in the next moment in time,’ says Dr Richard Williams, Lead Robotics Engineer at Dexory. ‘It does this around 100 times a second which is why it is so responsive to any changes in its environment. Once a decision has been made, it then commands the actuators in the base and tower to perform the desired action.’
‘We have programmed the robot to strive towards always being in a desired state,’ continues Williams. ‘So when it is following a path for example, it is continuously analysing how far it has deviated from that desired path. We then add control loops on top of that to ensure the subsystems perform the desired action correctly.’
‘For example, if the drive motors are using too much current, this could indicate an issue, so the robot will stop, check all of its systems and then if nothing is wrong, continue. This constant re-evaluation of the state of its systems and its surrounding environment contributes to the next decision, making it as accurate as possible.’
Conclusion
Dexory’s approach of combining unique mapping technology together with intuitive localisation and accurate obstacle detection has resulted in a truly automated inventory system. This autonomy means it can seamlessly integrate into the chaotic environment of any warehouse, no matter it’s size or stock type.
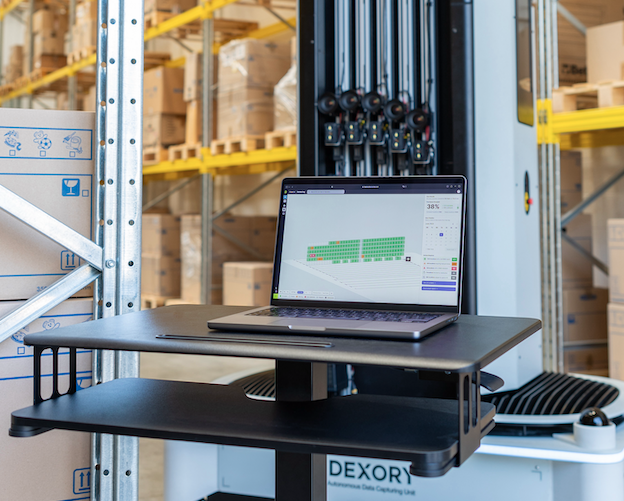
‘Every warehouse is completely different,’ concludes Scheunemann. ‘Warehouses can have very different aisle layouts, rack heights or types of machinery moving around. That’s why we have focussed on developing the robotics to be as intuitive as possible, so that the robot can adapt to whatever warehouse it is in, which is why we already have such a variety of customers,’ continues Scheunemann.
‘Our approach doesn’t require weeks to set up, or modifications to the warehouse. All we need is a few days to complete initial deployment, and the robot will run autonomously after that, reliably and safely scanning inventory whenever the customer requires.’
[1] 2016. Think Act - Of Robots and Men – in logistics [Online]. Roland Berger.
[2] 2019. 50,000 Warehouses to Use Robots by 2025 as Barriers to Entry Fall and AI Innovation Accelerates [Online]. ABI Research