Revolutionising warehouse management: Continuous full stock checks with DexoryView
January 11, 2024
In warehouse management, the challenges are as dynamic as the inventory itself. Traditional methods of occasional stock checks have proven to be time-consuming, prone to errors, and often result in operational inefficiencies. If you've ever found yourself grappling with misplaced items, tedious inventory counts, or the headache of lost goods, DexoryView's groundbreaking feature — automated full daily stock checks — offers the transformative solution your warehouse needs.
The challenge: Traditional stock checks and operational inefficiencies
Conducting periodic stock checks has long been the norm in warehousing. However, this approach poses several challenges:
- Inaccuracy and time-consumption: Traditional methods rely on manual counts, leaving room for human error and consuming valuable time and money.
- Misplaced items: Locating misplaced pallets, boxes, or items can be a daunting task, leading to delays in production and shipment.
- Lost goods: Searching for lost goods can be a logistical nightmare, impacting picking, replenishment, and overall warehouse efficiency.
The solution: Continuous full stock checks
Meet DexoryView's feature — Full daily stock checks. Here's how this autonomous solution addresses the challenges faced by warehouses:
1. Real-time data collection with autonomous robots
- Dexory's autonomous data-capturing robot eliminates the need for manual stock checks.
- Scanning assets on racks and shelves, the robot reads barcodes, QR codes, and data matrix codes with unparalleled accuracy and speed - up to 100,000 locations a day.
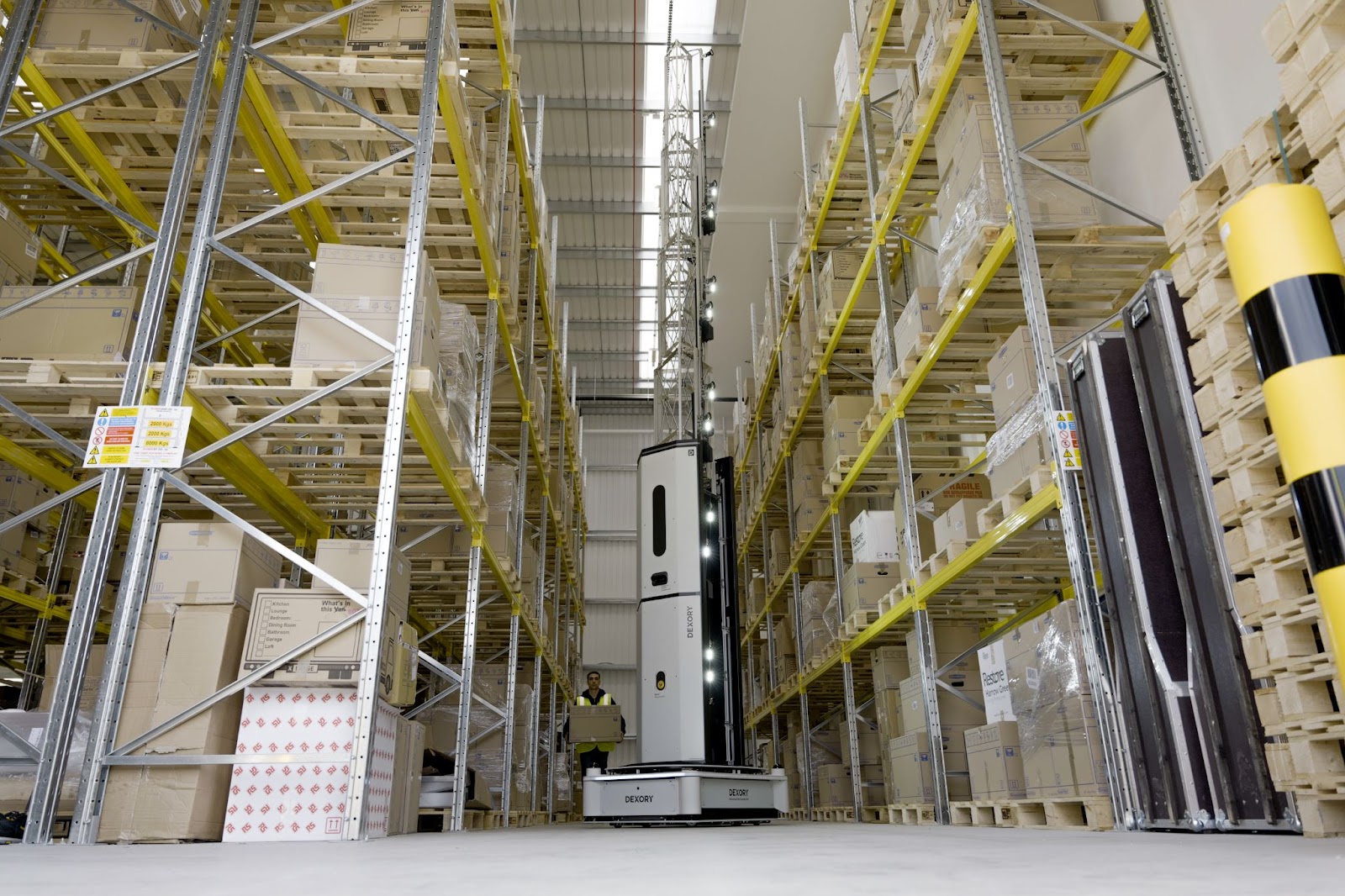
2. Precise goods allocation
- Pallets and boxes with labels are instantly detected and accurately allocated to their respective locations.
- The system ensures the precise comparison of pallets, picks and blockstacks to the Warehouse Management System (WMS).
3. Instant identification of misplaced items
- Misplaced pallets, boxes, or items are identified in real time, allowing for swift corrective action.
- DexoryView flags these discrepancies at their correct locations, ensuring immediate attention from warehouse teams.
4. Error notification via DexoryView
- Teams gain instant access to errors and discrepancies via the DexoryView platform.
- This streamlined communication ensures rapid response and resolution, minimising disruptions in warehouse operations.
The benefits: Efficiency, productivity and precision
By adopting DexoryView's continuous full stock checks, warehouses can improve their operations and easily meet contractual stock checking requirements:
1. Efficiency over occasional checks
- Move from occasional stock checks to continuous inventory data, ensuring operations run at maximum efficiency.
- Boost productivity by eliminating the need for time-consuming and tedious manual counts.
2. Instant identification of misplaced items
- Swiftly identify and rectify misplaced pallets, boxes, or items, streamlining picking, replenishment, and shipment processes.
3. Optimised goods tracking
- Always know the exact location of goods, minimising search times and maximising resource utilisation.
4. Ad hoc location checks
- Locations can be checked remotely, providing flexibility and control as needed.
Client success stories: Dexory transforms Maersk's logistics with continuous full-stock checks
Maersk, an integrated container logistics and supply chain services company, faced challenges in optimising warehousing processes to meet the evolving needs of the industry. Seeking innovation and efficiency, Maersk collaborated with Dexory, integrating an AI platform and autonomous robots into its warehouse operations in Kettering and Tamworth, UK. The results were transformative:
- Reduced WMS errors by 4% in one week: Dexory's real-time insights and automated solutions immediately addressed and minimised errors in Maersk's warehouse management system, enhancing overall accuracy.
- Saved hundreds of hours each year: The implementation of Dexory's solution significantly accelerated the process of locating items, resulting in a daily time savings of 2 hours per day on average.
- Improved customer experience and reputation: By streamlining logistics operations and ensuring accuracy, Maersk experienced an enhancement in customer satisfaction and an improved industry reputation.
- 40+ hours per week saved by automating cycle counts: Dexory's automation capabilities led to substantial time savings, allowing Maersk's staff to focus on more strategic and critical tasks.
- Full inventory checks daily vs. once every 2 weeks: The solution transformed Maersk's approach to inventory management, enabling daily checks instead of the previous bi-weekly schedule.
- Minimised 8 hours per week spent looking for misplaced/missing goods: Dexory's real-time tracking and identification capabilities reduced the time spent searching for misplaced or missing goods, contributing to operational efficiency.
Read the full case study to learn more about how Dexory's real-time, automated insights solution transformed Maersk's logistics operations.
DexoryView — Transforming warehouse management
DexoryView's full stock checks feature offers a seamless blend of automation, data analytics, and operational excellence.
Ready to revolutionise your warehouse operations? Contact us at letstalk@dexory.com to learn more about DexoryView's transformative impact on pick-face fulfilment.