Leading the way in warehouse robot safety
September 30, 2024
Today, nearly 20% of all retail purchases are made online, which is expected to increase over the next few years [1]. This boom in eCommerce has triggered an exponential rise in the volume of goods transported across our planet, demanding warehouses to be larger, efficient and reliable.
With more goods, staff and machinery moving around a warehouse than ever before, safety has become even more of a priority. So how does Dexory’s inventory scanning robot navigate the chaotic environment of a warehouse safely?
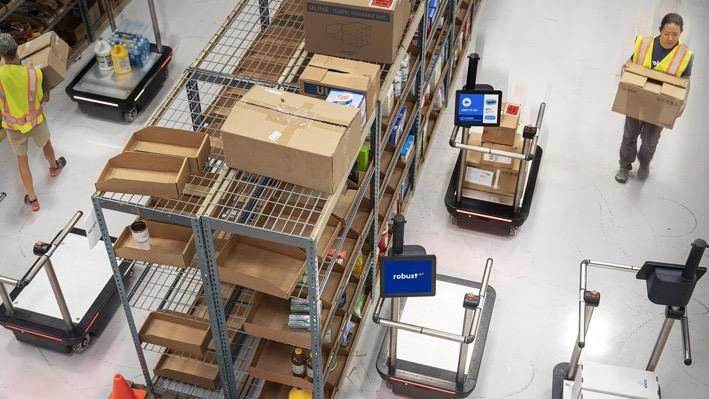
The different dimensions of autonomous robot safety
There are countless hazards within a warehouse, whether it’s the immediate risk of tripping over something, or the long-term risk of repetitive strain injuries from manually handling goods. Consequently, warehouses have to take a multi-dimensional approach to safety, to ensure the wellbeing of its staff.
‘Warehouses need to consider safety in different dimensions,’ reveals Guillaume Doisy, Lead Architect at Dexory. ‘Not only do you have horizontal safety, with objects moving around at ground level, but also vertical safety, as goods are stored in tall racks. This is particularly relevant when it comes to scanning inventory because you need visibility of every item of stock no matter where it is located.’
Taking stock
To keep track of goods, warehouses regularly complete a stock take or inventory scan. This provides the warehouse manager with information on every storage location in the warehouse, allowing them to understand the space utilisation of racks, ensure relevant stock is available to pickers and correct any errors.
The conventional approach to recording inventory involves manually scanning pallets by hand, which often requires lifting workers by forklift to reach goods stored at height. Forklifts are a major safety risk, with over 97,000 injuries caused by forklifts every year [2].
Alternatively, drones mounted with cameras can be used. This allows stock high up in the racks to be recorded easily without risking the safety of workers. However, if a fault occurs, the drone can fall, potentially harming staff. For this reason, aisles must be shut down when the drone is in operation which can significantly reduce productivity.
‘Our autonomous inventory scanning robot, on the other hand, is inherently safe, so it does not impact the activity of a warehouse,’ highlights Doisy. ‘It features an extendable tower which scans racks up to 14m, avoiding the safety risks associated with forklifts and drones. We have also integrated comprehensive perception systems and redundancy so that it detects and responds appropriately to any moving obstacle in any direction. This allows it to slot seamlessly into the day-to-day operation of a warehouse, without disruption.’
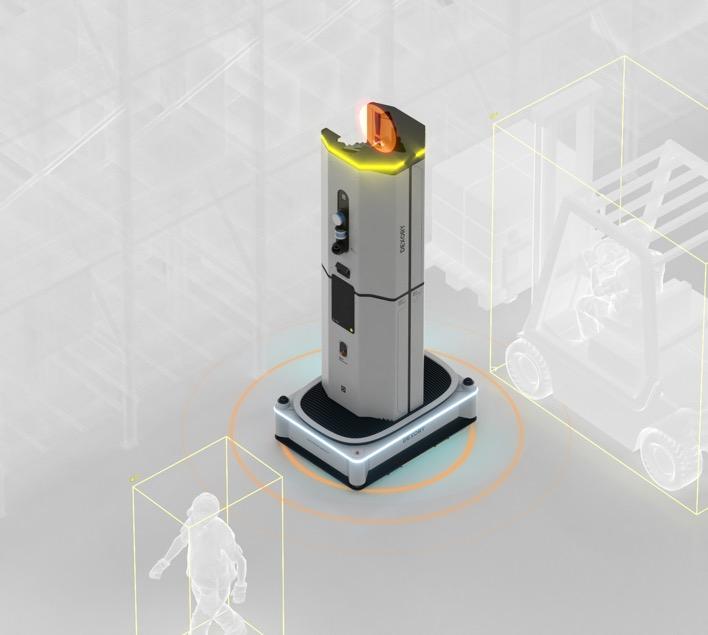
Dexory’s robot safety systems
Dexory have implemented several layers of safety into its autonomous robot. The first is a functional safety system which uses sensors, 2D and 3D lidars, as well as 3D cameras to continuously scan the robot’s environment as it moves around the warehouse. If an obstacle is detected within a certain range, the robot automatically calculates the deceleration required and brakes to avoid a collision. Therefore, the robot never gets close to an object that it can’t avoid.
On top of this lies an intuitive higher-level safety protocol which uses algorithms to anticipate risks and recalculate the robot’s trajectory to avoid obstacles. ‘The robot uses innovative mapping technology to generate a blueprint of the warehouse before it begins a scan,’ explains Doisy.

‘If it detects an obstacle on its planned route, it will reprogramme its path to avoid a collision, leaving plenty of margin. Our algorithms are so advanced that the robot can differentiate between different types of obstacles, so it leaves more of a safety margin if it detects a human, for example.’
However, if for some reason an error occurs within these calculations, the robot remains safe because the functional safety layer will always prevent the robot from colliding with any obstacle.
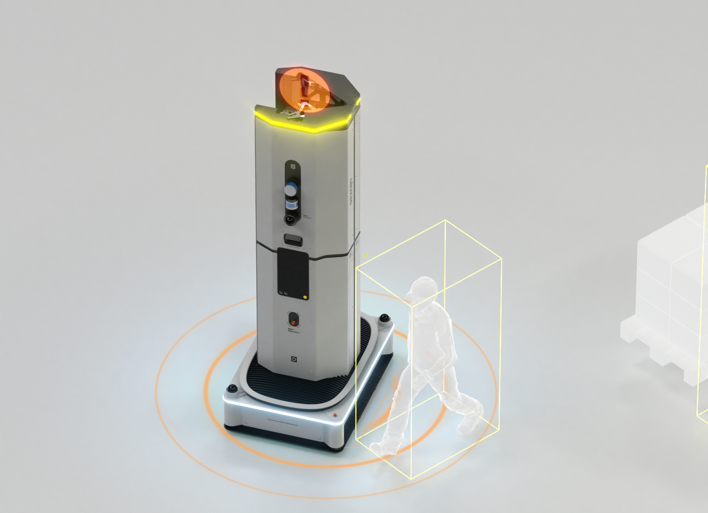
Multi-dimensional perception
The key to the robot’s multi-dimensional awareness is the fidelity of the data captured by the perception systems. The combination of 2D safety rated and 3D lidars on the base, along with 3D cameras and sensors on the tower allows the robot to perceive a field of view around 50 m [164 ft] horizontally and 25 m [82 ft] vertically.
‘The perception systems continuously scan a full 3D bubble around the robot, so any obstacle is instantly detected by at least three sensors at the same time,’ explains Doisy. ‘The multitude of sensors we use ensure a high level of redundancy, so even if a sensor fails, there are others in place to detect objects, guaranteeing safe operation. This, is particularly important when it comes to the protection of the extendable tower.’
Scaling the safety of the tower
To scan goods as high as 14 m, the Dexory robot features an innovative extendable tower which automatically extends and collapses according to the height of the aisle it is scanning. This capability also allows it to move autonomously through a warehouse, collapsing down to fit through any doorways.
However, to ensure the safety of the tower, the perception systems need to scale dynamically with the movement of the tower. This is achieved through scanning rails mounted with the various sensors which are connected to each of the tower’s lifting sections.
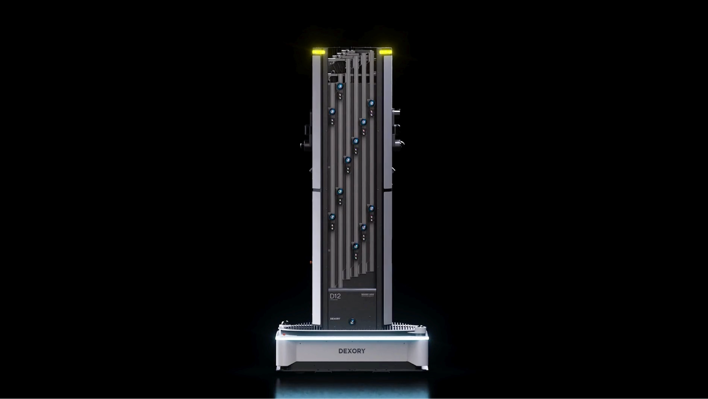
‘Extending this 3D safety capability for the entire height of the tower is what makes our robot so unique,’ adds Doisy. ‘Typical AMRs [Autonomous Mobile Robots] are not that tall, so only need to consider safety at ground level. Whereas we must adapt our detection based on the height of the tower and perceive the environment dynamically, with enough confidence to guarantee the tower’s safety.’
The rise of robots
The productivity benefits of warehouse automation is leading to a surge in AMR’s, with over 4 million robots expected to be deployed in 50,000 warehouses by 2025 [3]. This adds another safety challenge, as robots now need to work around other autonomous robots, without colliding.
‘Our robots are deployed in a number of sites where they are not the only autonomous machinery moving around the warehouse,’ says Doisy. ‘Although we are confident in the capability and adaptability of our robot, we cannot control the trajectories of others. This safety topic is becoming increasingly important - how do we validate our system to work in close proximity with other autonomous robots?’
‘As the adoption of AMR’s continues to increase, autonomous technologies must become more intelligent to ensure that robots can complete their individual tasks safely and effectively whilst sharing the same space,’ concludes Doisy. ‘Achieving this synergy between AMRs is going to be essential for arming warehouses with the productivity they need to meet the ever-growing demand of the logistics sector.’
References
[1] 2024. E-commerce as percentage of total retail sales worldwide from 2021 to 2027 [Online]. Statista
[2] G.B., 2018. Local Emphasis Program for Powered Industrial Trucks [Online]. OSHA
[3] 2019. 50,000 Warehouses to Use Robots by 2025 as Barriers to Entry Fall and AI Innovation Accelerates [Online]. ABI Research