How to improve inventory accuracy in a warehouse: 5 strategies for success
February 4, 2025
If you've ever had to deal with missing stock, miscounts, or frustrated customers due to incorrect inventory data, you’re not alone. Keeping inventory accurate in a warehouse can feel like a never-ending challenge, especially when operations scale up and order volumes increase.
But here's the good news: there are practical, proven ways to improve inventory accuracy without slowing down your workflow. In fact, the right strategies can actually save time, reduce waste, and boost warehouse efficiency.
In this article, we’ll walk through five key strategies that help warehouses like yours maintain 99.9% inventory accuracy, minimise human error, and make stock tracking seamless.
1. Implement real-time inventory tracking
Let’s start with the most powerful change you can make: real-time inventory tracking. If you’re still relying on manual stock checks or outdated spreadsheets, you’re leaving too much room for error.
The key to accuracy is knowing where every item is at any given time, not just once a week or at the end of the month. That’s where automation and digital tracking come in.
How to achieve this:
- Automated stock-scanning robots: If you had a robot scanning your shelves daily, how much more confident would you feel about your inventory data? Automated stock scanners ensure every item is accounted for, reducing reliance on manual checks.
- Barcode tracking: Barcode scanners improve visibility, making stock movement easier to track. They also reduce picking errors and speed up order fulfilment.
- Cloud-based inventory management: Using a system that updates in real-time means that every department—warehouse, logistics, sales—sees the same up-to-date stock levels, preventing miscommunications.
Real-world impact: Warehouses using DexoryView and stock-scanning automation achieve near-perfect inventory accuracy with real-time data collection, reducing stock discrepancies by over 90%.
Explore how Yusen Logistics improves visibility and efficiency with DexoryView
2. Conduct regular and automated cycle counts
Relying on a once-a-year full inventory audit is risky. By the time errors are found, they’ve likely caused weeks or months of operational issues.Instead, warehouses that achieve the highest inventory accuracy rely on regular cycle counts. This means checking different sections of inventory on an ongoing basis, so errors can be spotted and corrected before they cause disruptions.Best practices for cycle counting:
- ABC analysis: Not all stock is equal. Prioritise high-value and fast-moving items (Category A) for frequent cycle counts, while lower-priority stock (Categories B & C) can be counted less often.
- Automated cycle counting: Manually counting stock is time-consuming and prone to mistakes. Using robots or AI-driven inventory checks ensures accurate, unbiased results without human error.
- Random spot checks: High-risk stock locations, such as return areas or frequently accessed shelves, should be checked more often to prevent accumulating errors.
Discover how Maersk improved their inventory accuracy to 100% in a few weeks
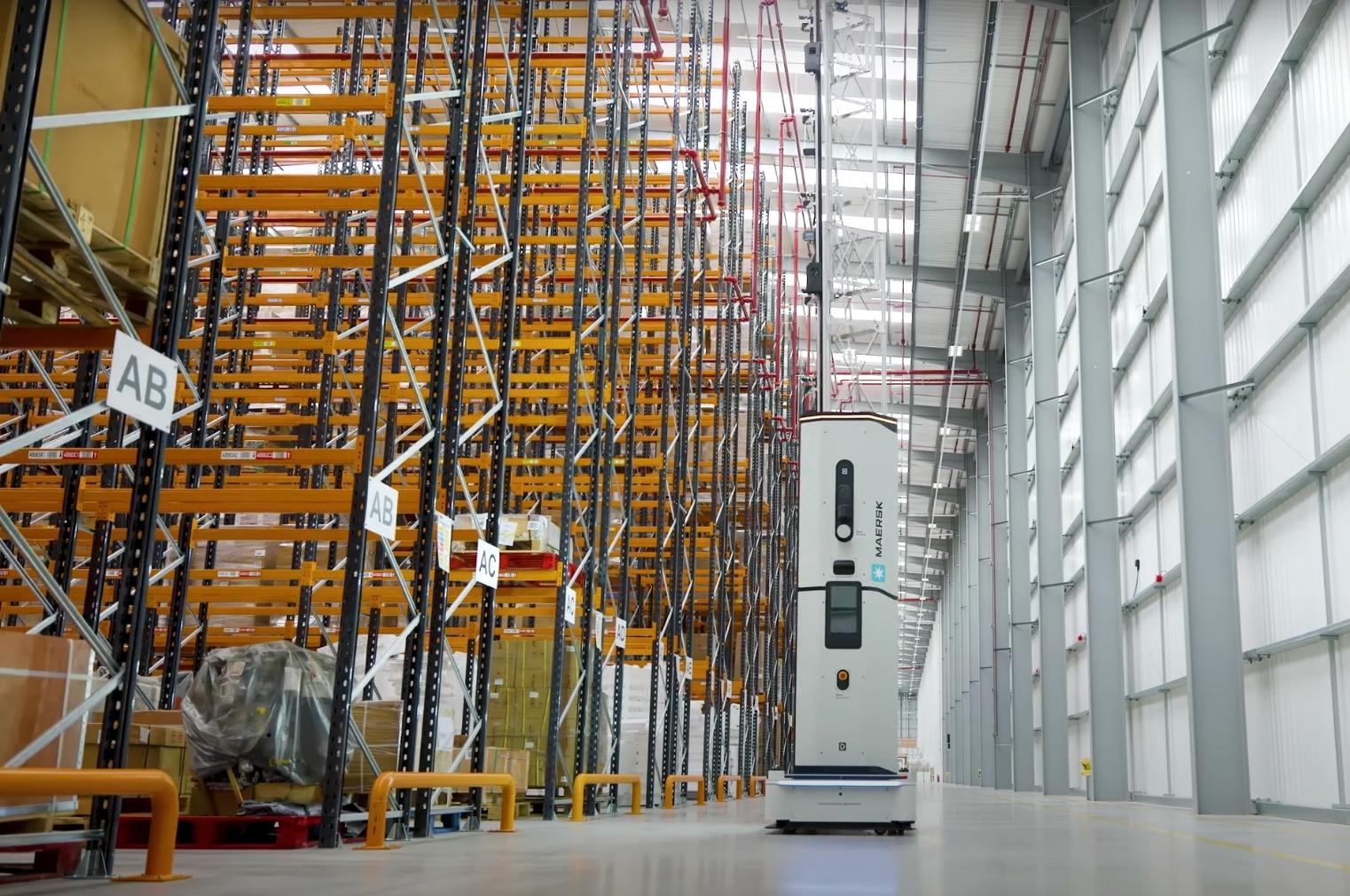
3. Improve warehouse organisation and layout
Even with the best tracking systems, a disorganised warehouse makes mistakes more likely. A cluttered or inefficient layout leads to misplaced stock, incorrect picks, and slower fulfilment times.How to improve organisation:
- Slotting strategy: Place frequently picked items in easy-to-reach locations, while low-turnover items can be stored in less accessible areas.
- Clear signage and labelling: Every aisle, bin, and shelf should be clearly labelled. Misplaced stock is often the result of unclear location markers.
- Fixed vs. dynamic storage: Some warehouses benefit from fixed storage locations, where each SKU has a designated place. Others use AI-driven dynamic storage, where stock is placed based on movement patterns.
Pro tip: Use warehouse simulation software to test new layouts before physically rearranging anything, saving time and reducing operational disruptions.
4. Minimise inventory handling errors with standardised processes
Even with advanced systems in place, human errors in stock handling remain one of the biggest causes of inventory discrepancies. From misplaced items to incorrect stock adjustments, these small mistakes can add up to major inefficiencies.To achieve near-perfect inventory accuracy, it’s essential to standardise processes, reduce unnecessary handling, and introduce built-in checks to catch errors before they escalate.How to reduce handling mistakes:
- Enforce a ‘Scan Everything’ policy: Every stock movement (inbound, outbound, and internal transfers) should be scanned and recorded in real-time. This ensures that no item is misplaced or miscounted.
- Introduce error-proofing (Poka-Yoke) techniques: Mistake-proofing methods like barcode scanning validation, pick-to-light systems, and automated alerts can help employees avoid mispicks and misplacements.
- Implement a two-step verification for stock adjustments: Any manual changes to inventory levels should require a second review to catch potential input errors.
- Use visual cues for stock accuracy: Colour-coded shelf labels, digital displays, and AI-powered vision systems can make it easier to identify stock location errors at a glance.
Real-world example: Even with strict processes, warehouses often struggle with misplaced stock and unnoticed discrepancies. DexoryView helps eliminate these issues by:
- Providing automated stock checks: Dexory’s autonomous robots conduct wall-to-wall inventory scans to verify stock locations and ensure items are where they should be.
- Identifying discrepancies before they cause issues: If an item is placed in the wrong location or missing, DexoryView flags the issue immediately, reducing the need for lengthy investigations.
- Minimising manual adjustments: Instead of relying on warehouse staff to detect stock errors, DexoryView automates the verification process, reducing human intervention and preventing accidental data entry mistakes.
See how it works:
5. Reduce human errors with robotics and automation
Even the best employees make mistakes, especially when pressure is high and order volumes surge. Human errors account for a major portion of inventory inaccuracies, from incorrect data entry to mispicked items.This is why warehouse automation is becoming essential for accuracy.Key technologies to consider:
- Autonomous Mobile Robots (AMRs): Robots can autonomously scan and validate stock, ensuring discrepancies are caught before they impact order fulfilment.
- AI-powered vision systems with robots: AI-based cameras detect misplaced stock and flag errors instantly.
- Automated order picking: Pick-and-place robotic systems reduce mispicks, increasing accuracy and fulfilment speed.
Did you know? According to a report by 6 River Systems, "Automated and efficient warehouses in the survey were 76% more likely to boost inventory accuracy to 99% or higher."
Final thoughts: Accuracy = profitability
Keeping warehouse inventory accurate is all about building a more efficient, profitable operation. By implementing real-time inventory tracking, automated cycle counting, warehouse layout optimisation, warehouse robotics, and more, you can eliminate stock discrepancies, cut costs, and improve fulfilment speeds.Next stepsIf you’re looking to make inventory accuracy effortless, it’s time to consider automation. Dexory’s AI-powered warehouse intelligence platform helps warehouses achieve unmatched accuracy and efficiency with real-time data insights.
Get in touch today to see how it works
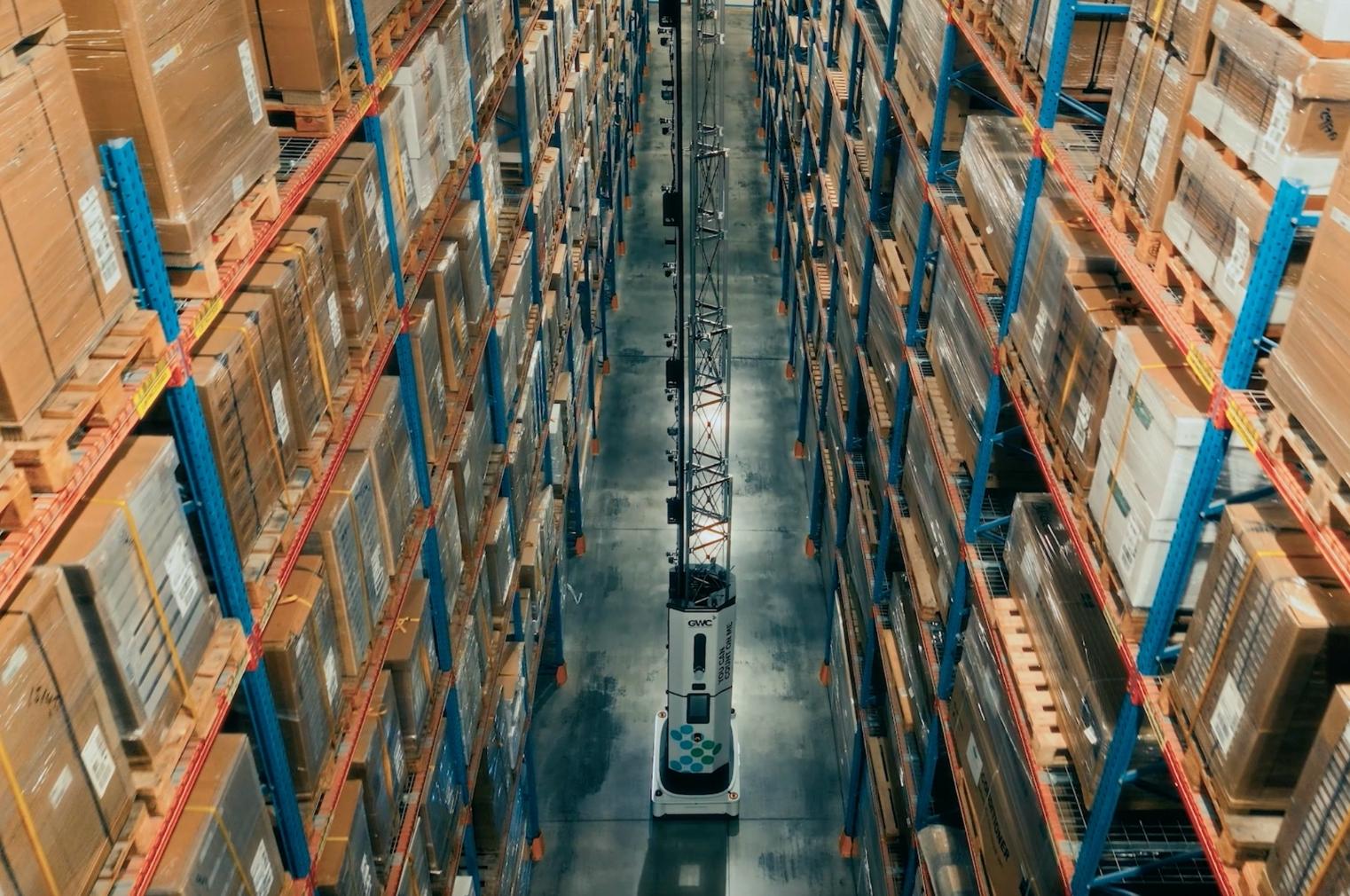