Boosting warehouse efficiency with automated inventory management systems
February 6, 2024
The need for efficiency
Over the last few years, the surge of e-commerce has led to a paradigm shift in supply chain, manufacturing and logistics, which is now one of the fastest growing industries in the world [1]. This has led to an exponential increase in the global volume of goods, all of which require manufacture, warehouse storage and transportation.
In fact, for every $1.2 billion spent online, an additional 775,000 sqft (72,000 m²) of warehouse space is needed [2]. With global e-commerce sales expected to rise to £6.4 trillion by 2026, [3], the race for space is well and truly on.
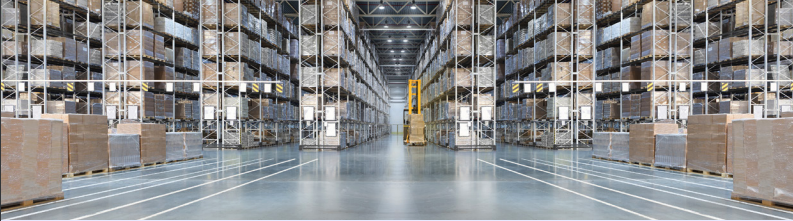
Alongside this, warehouses are also having to find new approaches to efficiently manage this increased number of goods whilst meeting the demand for faster delivery times. This has escalated the need for manufacturing staff, yet the labour market is not keeping up. Over 41% of manufacturing jobs lost during the pandemic are still to be recovered. While in the US, up to 2.1 million manufacturing jobs could go unfilled by 2030 [4].
This combination of increased goods, quicker turnaround times and staff shortages is driving a lack of visibility which is costing companies billions of dollars [5]. So how can companies improve their warehouse space optimization and efficiency?
Warehouse optimization using real time data
The key to surviving this constantly changing landscape lies in real time data insights. By understanding the end-to-end journey of goods, companies can have more control over inventory, ensuring the most relevant stock is always available to pickers. Whilst visibility of the space utilisation of racks can highlight opportunities to merge stock and maximise space, reducing the need for additional warehouse units.
‘Data can be used to build an accurate picture of the warehouse in real time,' highlights Andrei Danescu, CEO of Dexory. 'This arms managers with the latest knowledge, allowing them to make more informed decisions, solve issues sooner and optimise the overall layout and operation of the warehouse.’
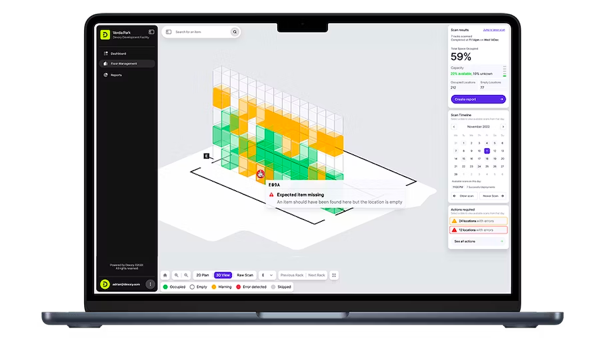
‘Our solution captures more data, at higher accuracies and faster rates than any other stock-scanning device on the market. We achieve this through a pioneering approach that combines autonomous robot technology with a digital twin platform.’
The Dexory solution to warehouse inventory control
The Dexory autonomous system consists of two main elements:
- A fully Autonomous Mobile Robot (AMR) which captures warehouse data by daily scanning the entire warehouse.
- A software intelligence and visibility platform called DexoryView which interprets and visualises this data. DexoryView gives users complete access to the deep insights and aggregated data feeds from all the warehouses they operate.
The robot is essentially made up of a 12 m (40 ft) mechanically extending tower which sits on top of an autonomous base. The tower is instrumented with a combination of cameras, sensors and lidar technology which enable it to scan every row within a rack simultaneously.
The autonomous base features a proprietary and bespoke software stack which allows the robot to quickly map, localise and navigate its way around a warehouse, regardless of the size or shape. It also uses a series of cameras and lidars to automatically avoid obstacles, whether that be at ground level or high up in the racks. This means the robot can run safely during normal warehouse operating hours, capturing data when it is needed most.
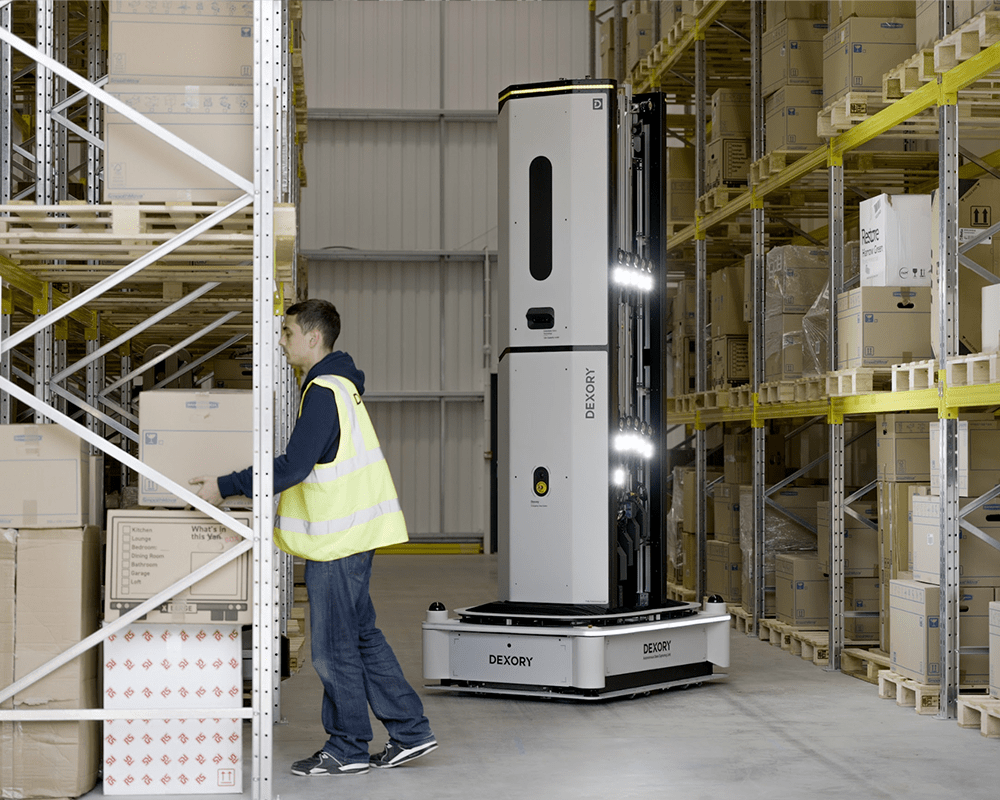
‘The ability to scan entire racks in one go means we have the highest scanning capacity than other solutions,’ highlights Danescu. ‘Typical stock-scanning drones can achieve around 400 pallets per hour, but we scan on average 8,000 to 9,000 pallet locations and have gone up to 15,000 locations with a single robot. This allows us to scan an entire warehouse in a day and provide daily insights to managers which gives them a much more accurate overview of what’s going on.’
This data is fed into DexoryView in real time, along with information from the Warehouse Management System (WMS), to reconstruct an accurate 3D representation of the warehouse. This allows warehouse staff to view the latest images, 3D data and analytics of every location within a warehouse. The platform then uses machine learning techniques to suggest space and positioning optimization strategies to help improve warehouse efficiency.
‘We are providing warehouse managers with information they have never had access to before,’ says Danescu. ‘They can now understand not just how full the warehouse is, but also how full each pallet is. Our analytics also help them with demand forecasting and identifying bottlenecks so that they can optimize space and run an efficient warehouse.'
How Dexory's automated warehouse inventory management works
To fully understand how the robot scans a warehouse, let’s run through an example. Firstly, the robot will create a global map of the entire warehouse, so that it knows its position at any point in time. This is typically completed in a few hours during the initial set-up phase when the robot is first installed.
The robot remains stationed at its dock until it receives a command from either the predefined schedule or from the warehouse manager to begin a scan. The 3D cameras and multiple 360 deg lidars on the tower as well as the 360 deg lidars on the base will then map the environment surrounding the robot. This information is overlaid with preferred operating trajectories, and if the robot concludes it is safe to move, it begins to follow its route to the first aisle of the scan.
‘The combination of lidars and 3D cameras help the robot identify any obstacles in its path both horizontally and vertically,’ explains Jorge Lozano, Head of Special Operations at Dexory. ‘If it comes across an obstacle, it will ‘see’ it, automatically recalculate a route around it and continue scanning.'
'However, if the obstacle is large and requires the robot to move too far away from the racks to capture accurate information, it will pause scanning and flag this in the digital platform. This ensures that only reliable information is fed to DexoryView. We’ve also implemented safety lidars on the base, so that if any obstacles suddenly appear, the robot immediately stops.’
When the robot has navigated to the beginning of the first aisle, lidars on the tower scan for any obstacles above the robot. If clear, the tower automatically extends to the height of the racks in a few seconds, and once in position, begins to move down the aisle at a fast-walking pace.

‘As the robot moves, the lidars, cameras and lights all the way up the tower start scanning,’ highlights Lozano. ‘Lidars capture point cloud data to measure the volume of each pallet, while the cameras scan barcodes and take high resolution images. All this information is fed to DexoryView via a continuous feed.’
Once the robot has scanned the entire aisle, it turns round and scans the other side. When both sides of the aisle have been completed, the robot moves to the next aisle. If it comes across any doorways or height restrictions on route, it automatically collapses the tower back down.
‘We have developed our robot to be completely autonomous in highly dynamic environments, so it doesn’t require any interaction from staff and the warehouse doesn’t need to be modified in any way,’ says Danescu. ‘Our localization techniques and perception technology mean that we don’t need any markers on the racks, on the floor or any other special environment enhancement. All our robot needs is a 2 m by 2 m space with access to a standard plug for its docking station and it will take care of the rest.’
The power of warehouse visibility
The accuracy, speed and visualisation of Dexory’s stock scanning robots is already proving invaluable to a number of major manufacturing companies. Maersk reduced WMS errors by 4% and saved around 2 hrs a day when locating items in just one week of using the Dexory robot. While Denso increased the accuracy of its stock taking to over 99% which helped them reduce production delays to zero.
‘Our vision doesn’t stop there,’ concludes Danescu. ‘We want to create a fully integrated platform that uses more intelligent AI to better support warehouse employees. For example, if 500 pallets are going to be delivered, we want our system to propose the optimum warehouse layout, the number of shifts required and the work instructions for that delivery. This will allow managers to focus on the more complex issues that they have to deal with.’
‘We also want to instrument the tower with more sensors,’ continues Danescu. ‘As it is 12 m [40 ft] in the air, we can measure temperature, humidity and other conditions, providing important intel for manufacturers of perishable goods. This gives them visibility on the best locations to store specific products to maintain quality and reduce waste.’
‘Overall, the combination of accurate data capture, real-time visualisation and autonomy of our technology means that we can help warehouses of any shape or size, storing any type of goods, in any part of the world boost their performance and efficiency.’
References
[1] J.O.D., 2023. AI, cannabis, and health food are among the 9 industries with promise for business owners this year [Online]. Business Insider
[2] 2021. The size and make-up of the UK warehousing sector – 2021 [Online]. UKWA.
[3] S.C., 2021. Retail e-commerce sales worldwide from 2014 to 2026 [Online]. Statista.
[4] 2022. The importance of manufacturing industry diversity [Online]. Deloitte.
[5] 2022. A.P. Moller - Maersk and IBM to discontinue TradeLens, a blockchain-enabled global trade platform [Online]. Maersk.