How to avoid stock discrepancies: Why they happen and how to stop them
March 10, 2025
Stock discrepancies are one of the biggest challenges in warehouse management. They lead to inaccurate inventory counts, inefficiencies in order fulfilment, and ultimately, dissatisfied customers. Whether you manage a large distribution centre or a smaller warehouse, ensuring inventory accuracy is critical to maintaining smooth operations and maximising profitability.
In this guide, we'll walk you through the key strategies to prevent stock discrepancies, improve inventory accuracy, and create a more efficient warehouse.
Understanding stock discrepancies
A stock discrepancy occurs when the actual inventory in your warehouse does not match the recorded stock levels in your warehouse management system (WMS). These discrepancies can stem from human error, process inefficiencies, theft, or system failures.
The consequences of stock discrepancies include:
- Delays in order fulfilment
- Increased operational costs
- Reduced customer trust
- Inaccurate financial reporting
By taking proactive steps, you can significantly reduce these errors and maintain accurate stock levels at all times.
1. Implement real-time inventory tracking
One of the most effective ways to avoid stock discrepancies is through real-time inventory tracking. Relying on periodic stock counts or manual data entry leaves room for errors. Instead, consider adopting automated inventory solutions such as:
- Stock-scanning robots: Autonomous robots that scan shelves regularly to update inventory data.
- Barcode and RFID tracking: Ensuring every item is scanned at key points in the supply chain.
- Inventory tracking software: A system that provides real-time updates and prevents duplicate or missing entries.
Many traditional warehouse management systems (WMS) still rely on periodic, quarterly, or yearly stock counts, leaving room for significant discrepancies due to human errors, misplaced stock, or outdated records. Implementing real-time tracking means you ensure that your inventory records remain accurate and up to date.
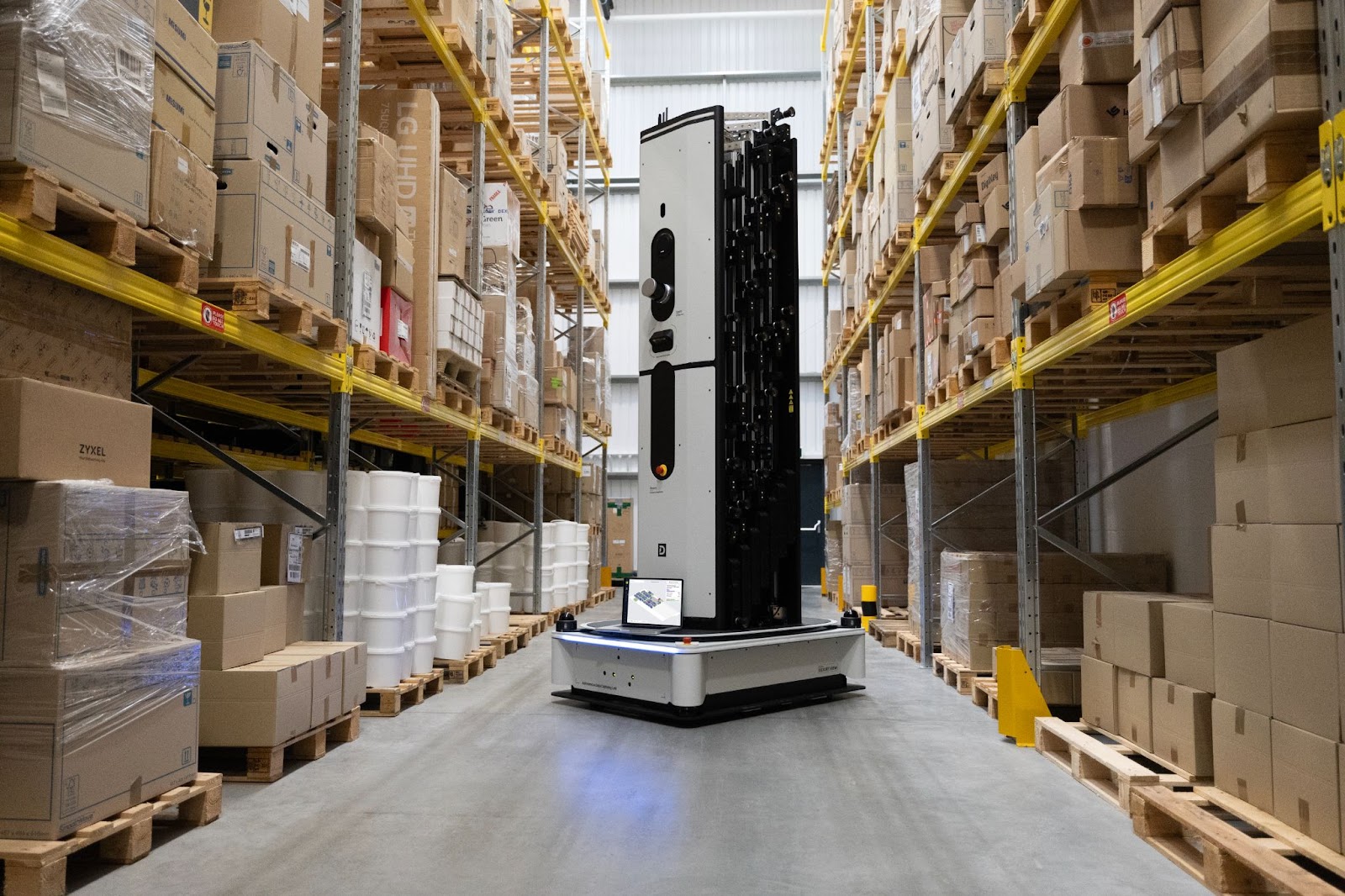
Dexory’s stock-scanning robot autonomously tracks warehouse inventory, ensuring real-time accuracy and reducing stock discrepancies. But its role goes beyond just scanning stock, it turns warehouse teams into data analysts. The data collected is instantly processed and compared with existing systems, feeding directly into DexoryView’s intuitive digital twin platform. This enables warehouse teams to focus on analysing patterns, predicting trends, and making data-driven decisions rather than manually searching for misplaced inventory.
2. Standardise and enforce inventory management procedures
Clear and consistent inventory processes reduce human error and improve efficiency. Ensure that you have standard operating procedures (SOPs) in place for:
- Receiving stock: Verify all incoming stock against purchase orders before recording them in the system.
- Picking and packing: Use system-generated pick lists to minimise selection errors.
- Stock replenishment: Implement a structured approach to restocking to avoid misplaced inventory.
- Returns handling: Have a process in place to track returned stock and update inventory records accordingly.
Enforcing these procedures ensures every team member follows best practices, reducing the likelihood of discrepancies.
3. Conduct regular cycle counts (daily if possible!)
Instead of waiting for year-end stock takes, conduct regular cycle counts to detect and correct discrepancies early. Daily cycle counting is the most effective way to prevent errors from accumulating over time. When an error occurs on day one and goes unnoticed, it can snowball into larger inaccuracies, affecting stock levels, order fulfilment, and overall inventory control. By catching mistakes immediately, you prevent errors from compounding and ensure that stock records remain accurate.
Key tips for effective cycle counting:
- Prioritise high-value or fast-moving stock for more frequent checks.
- Use technology like autonomous robots to automate counting.
- Rotate through different product categories to ensure full coverage over time
Frequent cycle counts help identify and address stock issues before they become major problems, ultimately improving your inventory accuracy and operational efficiency.
4. Minimise human error through automation
Human error is one of the leading causes of stock discrepancies. To reduce manual mistakes:
- Automate data entry: Reduce reliance on manual inputs by integrating your WMS with scanning solutions.
- Implement AI-powered analytics: Identify patterns in stock discrepancies and correct errors before they escalate.
By automating these processes, warehouse workers shift from physically verifying stock to analysing real-time data trends, identifying potential risks before they cause major disruptions, and optimising warehouse operations.
5. Train your team properly
Even the best systems will fail if your team isn’t properly trained. Ensure your warehouse staff understand:
- The importance of accurate stock records.
- How to use the equipment correctly, either scanners or autonomous robots.
- Standard procedures for receiving, picking, and shipping inventory.
- The process for reporting discrepancies when they arise.
Regular training sessions help reinforce best practices and improve overall efficiency.
Our tip: To manage stock discrepancies effectively, set up a clear and structured reporting system. Make sure every discrepancy is logged in a central system with key details like the date, time, affected stock, and possible causes. Encourage your warehouse workers to report issues immediately instead of waiting for the next stock count. Assign a dedicated person or team to investigate and resolve discrepancies quickly. With real-time inventory data available, teams can use analytics tools to track trends and refine warehouse processes, moving away from reactive problem-solving toward proactive decision-making.
6. Improve stock organisation and labelling
A cluttered or disorganised warehouse increases the likelihood of inventory mistakes. Ensure your warehouse layout is:
- Clearly labelled with barcodes.
- Organised logically based on picking patterns.
- Regularly tidied and maintained to prevent misplaced stock.
Having a structured storage system improves picking accuracy and minimises errors.
7. Use Digital Twins for warehouse optimisation
A digital twin is a virtual replica of your warehouse that allows for real-time monitoring of inventory movements. By integrating digital twins with AI-powered analytics, you can:
- Predict potential stock discrepancies before they occur.
- Optimise storage space for better efficiency.
- Improve demand forecasting and replenishment strategies.
By using digital twins, warehouse operators transition from manual stock management to data-driven analysis, identifying trends, inefficiencies, and potential bottlenecks before they impact operations.
Final thoughts
Stock discrepancies can be a major challenge, but with the right strategies, they can be minimised or even eliminated. By leveraging automation, enforcing standard procedures, and continuously monitoring your inventory, you can maintain accurate stock levels, improve efficiency, and enhance customer satisfaction.
Taking a proactive approach to inventory management not only prevents discrepancies but also gives you a competitive advantage in the logistics and warehousing industry.
Start implementing these best practices today, and you’ll see the difference in accuracy, efficiency, and overall warehouse performance.