What every business leader needs to know about digital transformation in logistics
April 7, 2025
Digital transformation. A widely discussed concept, but what does it actually mean in logistics? Whether you’re managing global supply chains or overseeing a single warehouse site, the pace of change is undeniable.
In this article, we’ll break down what digital transformation really means for logistics and warehousing, why it’s not something to leave on the “future goals” shelf, and how forward-thinking leaders are already leveraging smart technology to unlock value today.
Let’s dig in.
Why digital transformation in logistics is more critical than ever
Logistics and warehousing have traditionally been seen as physical, manual operations. But in the wake of disrupted supply chains, labour shortages, and growing customer expectations, sticking to traditional methods just doesn’t cut it anymore.
Digital transformation refers to the integration of digital technologies into all areas of business operations, changing how you operate, delivering value to customers, and adapting to changing market demands. In logistics and warehousing, this often involves:
- Automation and robotics to handle repetitive tasks
- Real-time data capture and insights to inform decision-making
- AI-powered analytics for forecasting, recommendations, planning, and optimisation
- Digital twins and simulation tools for space management
- Cloud-based platforms for centralising operations and improving visibility
And the benefits? They’re not just theoretical. We’re talking real-world ROI in the form of:
- Up to 90% time savings on inventory checks
- Error reduction in stock handling
- Improved staff productivity and safety
- Greater agility in responding to demand fluctuations or supply chain issues
The key pillars of digital transformation in logistics
To transform operations successfully, business leaders need to think beyond “buying a bit of tech.” A strategic digital transformation journey typically rests on four key pillars:
1. Data visibility and intelligence
You can’t optimise what you can’t see. One of the biggest game-changers in logistics is the ability to capture accurate, real-time data from every corner of the warehouse.
From shelf-level inventory scanning robots to smart sensors tracking environmental conditions, modern solutions give you the single source of truth you need to make smarter, faster decisions. And when this data is centralised into a warehouse intelligence platform, you move from gut feeling to evidence-based actions.
💡 Pro tip: Look for solutions that integrate seamlessly with your existing WMS or ERP, interoperability is key to avoid data silos.
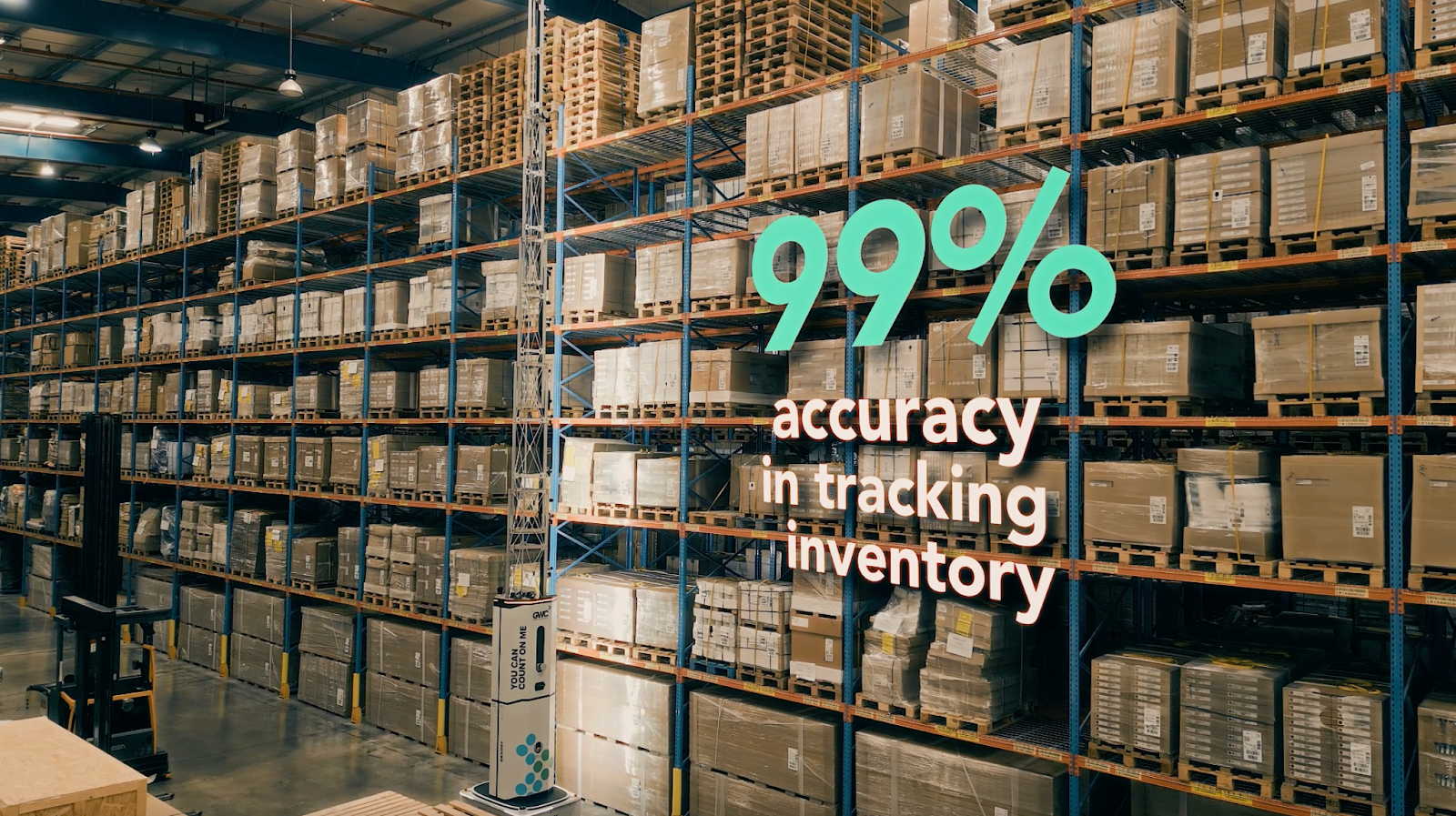
2. Automation without disruption
There’s a common myth that automation is complicated, risky, and disruptive. But the reality is that many solutions today are designed to be deployed in live environments, without halting operations.
Mobile robotics and AMRs, for example, can be installed in just a couple of weeks, and they work around your staff, not instead of them. This kind of flexible automation empowers teams to focus on higher-value tasks like quality control, exception handling, or continuous improvement.
3. Scalability and flexibility
Your needs today won’t be the same next quarter. That’s why scalable tech matters. Whether you're expanding your footprint, changing product lines, or reconfiguring your layout, your digital tools should flex with you.
Cloud platforms and subscription-based models help here, offering the ability to scale up (or down) without major capital expenditure. Look for partners that grow with you and offer continuous updates and support.
4. Culture and change management
Technology alone won’t deliver transformation, your people will. Change management is crucial, especially in environments where long-standing processes and mindsets might exist.
Make sure you communicate the ‘why’ behind the change, involve teams early, and provide training to build digital confidence. When employees understand how digital tools make their jobs easier, not replace them, you’ll get much stronger buy-in.
💡 Pro tips:
- Communicate the ‘why’: Help your teams understand how tech will support them. For example, AMRs can help them focus on managing exceptions or improving pick accuracy.
- Involve people early: Bring warehouse staff into the process from the start. They know what’s happening on the floor every day.
- Nominate digital champions: Empower team members to lead adoption.
- Offer hands-on training: Keep it simple, practical, and accessible.
- Celebrate small wins: Highlight early improvements to build momentum.
- Encourage feedback: Create space for input and adapt quickly.
Practical steps to get started with digital transformation
Starting your digital transformation journey doesn’t have to feel like stepping into the unknown. You don’t need to be a tech expert or rip up everything you’ve built, just take it one step at a time. Here’s a down-to-earth roadmap to help you move from intention to impact:
1. Audit your current operations
Before you bring in any new tools, take a good look at what’s already happening. Walk the floor. Talk to your team. Where are the bottlenecks? Which tasks feel clunky, manual, or error-prone?
Think bigger:
- Are pickers wasting time looking for misplaced stock?
- Do teams redo checks because the first results weren’t trusted?
- Are you losing sleep over stock discrepancies or delayed shipments?
Use this time to map out your daily workflows and spot the friction. Once you know where the pain points are, it becomes much easier to pinpoint where digital tools can help.
💡 Pro tip: Bring warehouse teams into this audit, they’ll often highlight issues you didn’t realise existed.
2. Define clear business outcomes
It’s easy to get swept up in shiny tech features. But digital transformation should always start with a business outcome in mind.
Ask yourself:
- Do we want to speed up fulfilment without hiring more staff?
- Are we losing money investigating stock errors?
- Do we need better visibility to plan our warehouse layout?
Having clear, measurable goals will help you filter through the noise and find solutions that make a difference. If you can link your goals to a tangible outcome, like reducing cycle counting time by 50% or cutting investigation costs in half, you’ll be in a strong position to get buy-in from senior stakeholders too.
💡 Pro tip: Tie each goal to a specific metric so you can prove ROI later.
3. Select the right partners
Not all technology partners are created equal. Some might have flashy interfaces, but little understanding of the day-to-day reality of running a warehouse. You need partners who “get it”, who know what it’s like to juggle deadlines, deal with space constraints, and keep operations running without disruption.
Look for providers who offer:
- Rapid deployment (think weeks, not months)
- Proof of value (ideally through pilots)
- Onboarding and support that go beyond installation
- Solutions built for live environments, so you don’t need to halt operations to make progress
And most importantly: pick people who feel like a long-term partner, not a short-term vendor.
💡 Pro tip: Ask for references from similar businesses, nothing beats real-world results.
4. Start small, then scale
You don’t need to roll out tech across every warehouse in one go. In fact, we wouldn’t recommend it. A pilot is your friend.
Choose one site, maybe the one with the most obvious challenges or the most enthusiastic team, and start there. Test, learn, and gather data. Prove the value. That success story becomes your blueprint for scaling across other sites.
What’s great about today’s tech (especially mobile robotics and cloud platforms) is that it’s modular and scalable. You can start small and build up as you grow, without needing to reinvent the wheel each time.
💡 Pro tip: Share results early and often. Small wins build confidence across your teams, and with your leadership.
Real-world impact: What leaders are saying
Some of the world’s most advanced logistics providers are already reaping the rewards of digital transformation. Here’s what leading organisations are achieving with automation and intelligent inventory insights:
- One major aviation logistics provider saved over 30 hours per week through automated inventory audits. They reduced errors by 70%, leading to fewer stock discrepancies, and cut “Unable to Locate” pallet issues by 50%, helping reduce unnecessary claims and improve customer satisfaction.
- A global contract logistics company achieved 98% putaway accuracy using automated validation tools. Within just 8 weeks, inventory accuracy improved by 5%, while manual stock investigations were reduced by 41%, freeing up operational time for higher-value tasks.
- A large international logistics operator increased inventory accuracy by 4% in just two months. Automated robots scanned up to 10,000 locations per hour, compared to 150 manually, transforming annual wall-to-wall audits into daily, automated checks.
- One 3PL saved 47 hours per week on empty location checks alone. Outbound errors dropped by 50+ per month, and the time spent on investigations fell from 24+ hours per week to just 10 hours, improving overall efficiency.
- Another logistics provider slashed monthly wall-to-wall stock counting from 100+ hours to just 2 hours a day, saving 205 hours annually. They also saw improvements in warehouse cleanliness and stock placement within just two weeks.
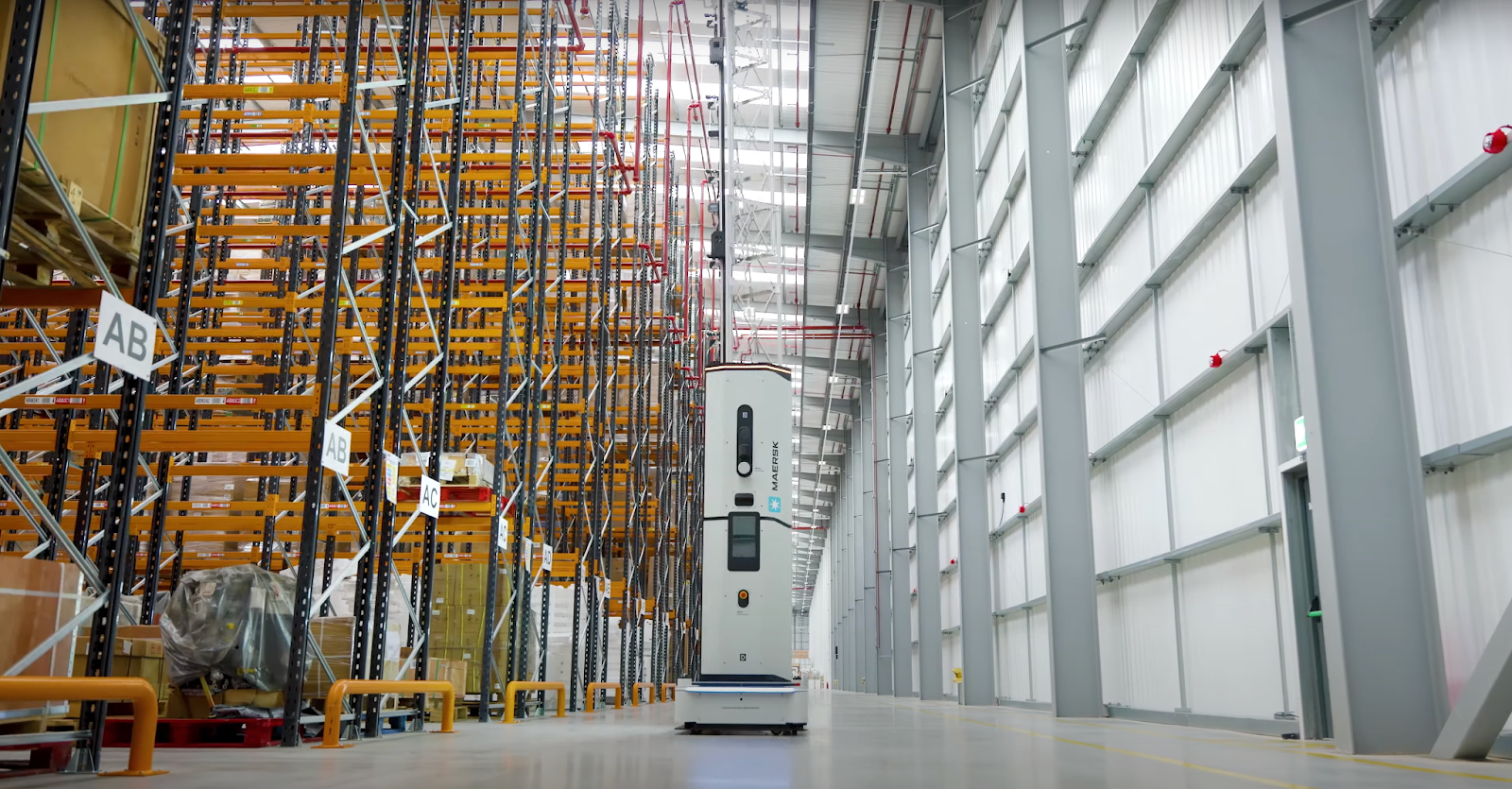
Final thoughts: Your next steps
Digital transformation doesn’t have to be complex, expensive or disruptive. Start small. Focus on value. Choose tools that evolve with you.
And above all, don’t go it alone.